Construction projects are complex endeavors that, without proper planning, can easily run over budget and schedule. That’s why having a reliable set of construction scheduling techniques is so essential.
Construction scheduling helps ensure construction projects stay on track and within budget. Implementing construction scheduling techniques before construction and throughout the entire project can also limit risks and delays, all while improving the overall quality of the effort.
In this blog, we dig deep into what construction scheduling is, explore different construction scheduling techniques, identify best practices for effective construction scheduling, and more.
Table of Contents
Understanding the Basics of Construction Scheduling
Construction scheduling involves the detailed planning of construction projects from start to completion. This can include pre-construction submittals/plans, physical construction, oversight, and project closeout, among other activities required by individual construction project contracts.
TA good construction schedule details who is responsible for tasks, when those tasks need to be done, and in what order they should be completed. Construction schedules also give project managers the details they need to equip their construction projects with the appropriate amount of people and equipment. With this information in hand, construction teams have a better chance of finishing a project more efficiently and correctly.
What is Construction Scheduling?
Construction scheduling involves compiling all the tasks and deliverables necessary to complete a construction project. Each deliverable is assigned a deadline and expected date of completion. Tasks are assembled in timeline order and are assigned to individuals.
Construction schedules serve as a “single source of truth” for the project. With a detailed construction schedule, construction teams and clients understand where things stand at all times. Thus, the schedule provides clarity into assigned roles, helps increase communication and collaboration, allows for more accurate budgeting, and allows clients to receive real-time updates on the status of their construction projects.
Key Components of a Construction Schedule
Construction schedules can be written or illustrated, depending on the preferences of the construction project manager and their team. Whatever the method, all construction schedules share some common characteristics, including:
- Tasks: The various tasks that need to be completed during construction
- Deadlines: When those tasks need to be completed and their expected durations
- Dependencies: Relationships between tasks that drive the project schedule
- Constraints: Issues that could cause deviation in the schedule
- Roles: The individuals or teams responsible for completing the tasks
- Milestones: Milestones signaling the end of a phase of the project. Milestones are different from deadlines, which are specific to certain tasks. Most construction schedules will have more deadlines listed than milestones.
Exploring Various Construction Scheduling Techniques
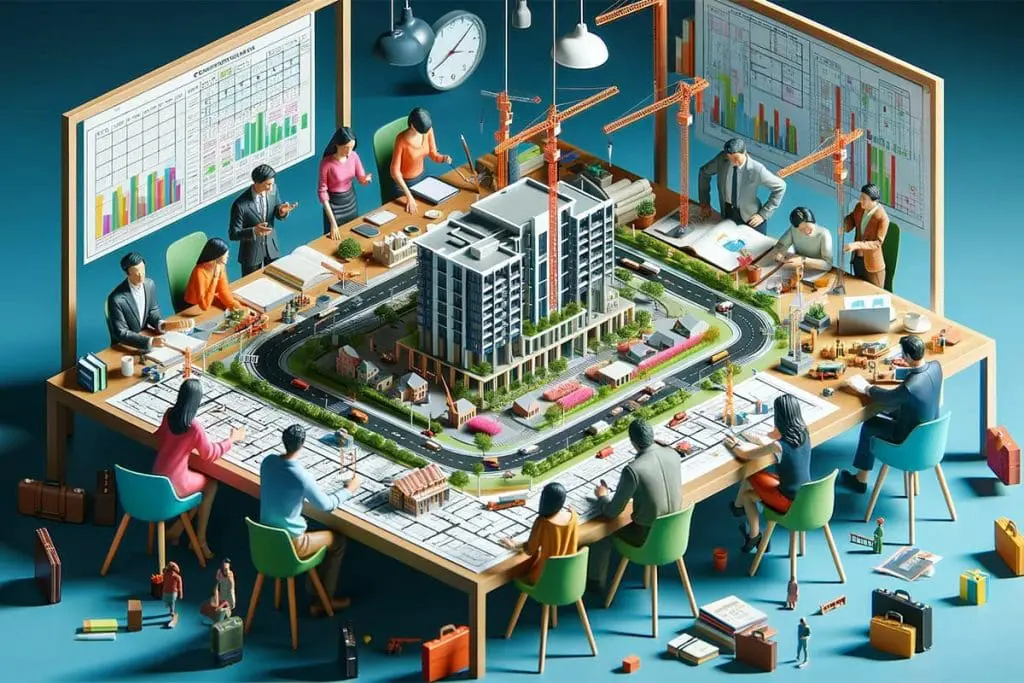
Though the goal and purpose of every construction schedule is the same, the ways in which construction schedules are created and implemented differ. Construction managers have a number of construction scheduling techniques to choose from for their projects. Among the most common methods are critical path, last planner system and pull planning, program evaluation and review, and Earned Value Management. Let’s review these methods.
Critical Path Method (CPM)
The critical path method (CPM) focuses on the tasks or activities that are most critical for the successful completion of a construction project. The construction manager identifies the minimum tasks required to complete a project using the CPM. Tasks are listed in terms of dependencies (i.e., Task B cannot be completed until Task A is done). The most urgent dependencies are then prioritized.
There are several steps involved in the CPM. They include:
- Identifying and listing all construction project tasks.
- Determining the order in which the tasks must be completed (including dependencies between tasks).
- Estimating how much time it will take to complete the tasks.
- Creating a network diagram that shows tasks, dependencies, and duration to complete tasks.
- Identifying the “critical path.”
The critical path is the list of tasks that will take the longest time to complete. Identifying these tasks is important, as any delay in any one task could result in the entire project running over schedule and over budget. Once these tasks are identified, the construction project manager will understand where to prioritize their team’s work.
The CPM offers many benefits, including:
- Allows managers to schedule activities around the most important tasks.
- Provides managers with the ability to schedule activities in a more efficient and effective manner.
- Provides visibility into which parts of the construction project might be more flexible (i.e., tasks that are not on the critical path).
- Offers a better chance that construction projects will be completed on time—thereby satisfying contractual obligations.
- Assurance of on-time invoicing upon completion of the construction project.
Last Planner System (LPS) and Pull Planning
The goal behind the Last Planner® System (LPS) is to make construction projects as lean and efficient as possible. Created by the Lean Construction Institute, the LPS “promotes the creation of a predictable workflow among various parties so that it achieves reliable results.” It does this by providing construction managers with a five-phase system that includes:
- Master planning: During this phase, the most important components of the construction project are identified, listed, and scheduled. These include major project milestones, tasks, and corresponding deadlines. The main goal or goals of the project are also determined to ensure that all tasks align with the client’s needs.
- Phase planning: In the second phase, processes are clearly defined, schedules are honed, and a final execution plan is created.
- Lookahead planning (AKA, “make-ready planning”): Here, all tasks are carefully reviewed by the construction managers (in this case, also known as “the last planners”), who look for any possible risks or obstacles that could stand in the way of the project being completed successfully and efficiently. Things they might look for include:
- The availability of labor and materials.
- Access to equipment.
- Other obstacles to construction, including conflicting documentation, time to receive required permits, etc.
- Weekly work planning: Construction teams review the tasks outlined in phase planning and create weekly work plans around those tasks. Each team is responsible for completing the tasks they’ve been assigned.
- Learning: During the final phase, construction teams analyze and measure the results of their work and learn from their findings in order to enhance and improve their processes. Learning is generally comprised of:
- Daily coordination meetings, during which last planners meet to discuss the overall performance of their teams and the status of the construction project. These meetings give planners the chance to proactively make adjustments as needed.
- Analysis of key performance indicators (KPIs) and metrics to ensure the project is on track to achieve its goals. KPIs that are often analyzed include the percentage of the plan that has been completed, the percentage of tasks that are ready to begin as planned, and the analysis of future tasks to begin planning for their implementation.
In addition to daily coordination meetings, many last planners augment their planning processes with daily huddles, where managers meet with construction teams to discuss that day’s tasks and deadlines. Huddles help teams stay on track. They also give them the opportunity to discuss potential issues before they arise and circumvent them before they have a chance to derail a project.
Finally, pull-planning is a component of the LPS in which resources – personnel, equipment, materials, etc. – only arrive at the construction site when needed. Think of it as a variation of the just-in-time inventory system that many plant managers use to align the receipt of raw materials with their production schedules. Pull-planning allows last planners to create a more efficient construction process by only receiving the required assets when they are actually needed.
Program Evaluation and Review Technique (PERT)
Construction project planners begin the PERT technique by identifying tasks within the project and their expected timeframes for completion. Managers then identify and prioritize the most critical tasks and create an estimated timeline that references the sequence of tasks, dependencies between tasks, and the expected time it will take to complete each task.
Note that while there is some overlap between the PERT method and CPM, they each serve slightly different use cases. The PERT is mainly used as a time estimation tool and is best applied when the timeframes for completion of tasks cannot be completely and accurately defined. The CPM is generally used when the timeline to complete tasks is more easily predictable (for example, based on the time it took to complete tasks in past projects).
Unlike CPM, a PERT schedule is always presented graphically. This is known as a PERT chart. Similar to a Gantt chart, a PERT chart displays the tasks and the order in which they must be completed in an easy-to-read diagram. PERT charts use arrows to show the direction of the construction workflow and mark each task with its expected completion timeline (for example, 2 weeks, 3 weeks, etc.). PERT charts may also show project milestones, call out dependencies between tasks, and more.
Earned Value Management
More of a project management methodology rather than a pure construction scheduling technique, Earned Value Management (EVM) is nevertheless important to ensuring projects remain on track. Also known as Earned Value Analysis, EVM employs three different values to calculate the status of projects: Planned Value (PV), Actual Cost (AC), and Earned Value (EV).
PV measures the amount of work that should be done by certain points in the schedule as well as by the completion of the project. It is measured using the mathematical formula % complete/planned x budget at completion = total planned value. It’s a good tool for measuring the value of the work being done as the project moves through its various phases.
AC shows the actual costs incurred during specific periods throughout the project. These costs accumulate through the lifecycle of the project, finally resulting in a total amount when the project reaches its conclusion.
EV monitors how much money should have been spent at each phase of the project, rather than how much was actually spent. It is calculated using the mathematical formula % complete x budget at completion = EV. It shows the monetary value of the work that’s been done up to a certain point.
EVM offers many benefits, including:
- Project forecasting and risk management. EVM allows construction managers to foresee problems before they occur, allowing them to course correct and avoid potential issues.
- Progress tracking. Construction projects can be closely monitored from start to finish, ensuring that work takes place on time and on budget. With EVM insights, managers can accelerate work, ramp up hiring, procure additional equipment, and more as necessary.
- Resource planning and forecasting. Managers can use EVM to see if their current resources are appropriate for the tasks they have planned. They can right-size resources to fit within the project scope and budget.
- Quantifying value. Managers can quantify the value of the work being performed through PV, AC, and EV – at any point during the construction process. They can then make decisions on how to improve the process if necessary.
The Role of Technology in Construction Planning
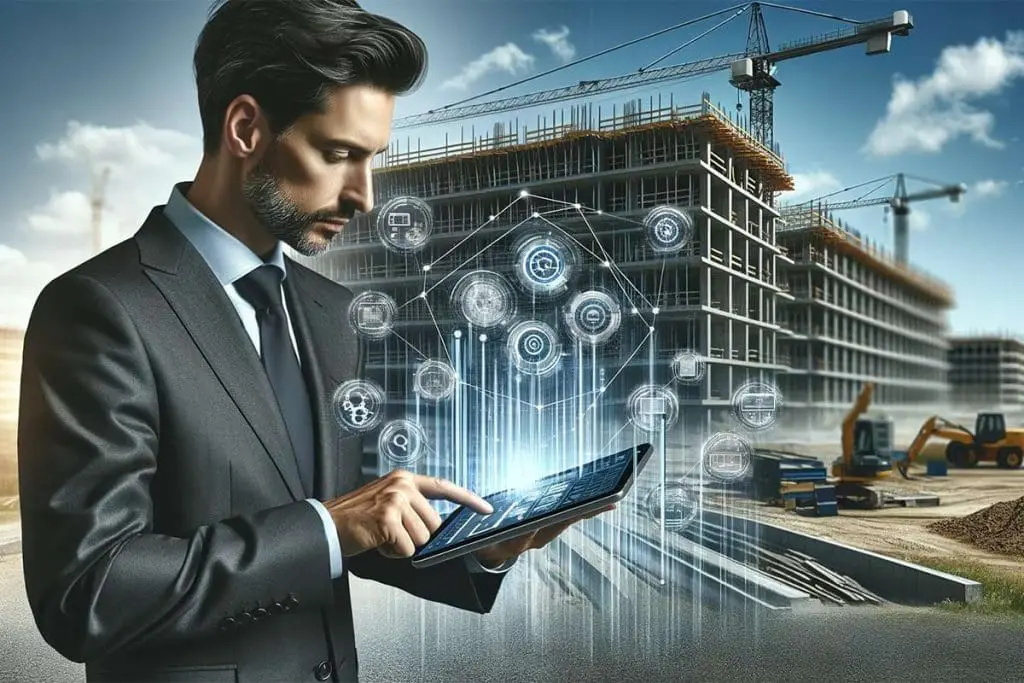
Technology plays a major role in modern construction planning. Construction projects are simply too large and complex for human beings to coordinate on their own. Technologies, including construction scheduling software, provide many benefits to help keep construction projects on time and under budget, including automation, better communication among teams, and more. These and other features simplify and optimize the scheduling process.
See how technology can optimize cost engineering in your projects. Read more about cost engineering in construction and boost your project’s efficiency and accuracy.
Advancements in Scheduling Software
Construction scheduling software has enjoyed many advancements over the past few years. Today, most construction scheduling tools are cloud-based and easily accessible via mobile devices, making it easier for project managers and planners to keep track of all phases of construction from anywhere.
One of the most popular construction scheduling tools is the Gantt chart. A Gantt chart is a bar chart that shows dependencies between tasks and allows project managers to create a visual hierarchy that shows the relationship between critical and less critical tasks. Many different software tools can be used to create a Gantt chart. Some of the most popular include Microsoft Project, Oracle Primavera P6, GanttPRO Project Planner, Smartsheet, and others.
The Project Evaluation and Review Technique employs a similar visual aid to display the relationship between tasks and their expected times for completion. Again, several software tools can be used to create PERT charts, including Microsoft Excel, Lucidchart, SmartDraw, and other popular workflow management tools.
Beyond charts, many other innovative technologies are increasingly playing a vital role in construction scheduling, including:
- Simulation tools, which allow construction project managers to simulate the impact a change to the task schedule will have on the construction schedule, costs, and the outcome.
- Building Information Modeling (BIM) and 4D scheduling, which can provide managers with digital representation of their projects. When linked with a construction schedule, they can provide a visual window in the progress of the construction project over time.
- Artificial intelligence (AI) and machine learning (ML), which are embedded in many modern construction technologies and can be used to automate the construction process, resulting in greater efficiencies.
Comprehensive project and portfolio management software incorporates many of these features to make it easier for managers to visualize and track the progress of construction projects. For example, Oracle Primavera P6 and Microsoft Project allow project managers to plan, manage, and execute all aspects of their projects, including scheduling.
Both tools have their unique benefits. Whereas each has features that align well with the CPM, Oracle Primavera P6 provides more in-depth functionality, including “what-if” scenario analyses that show what is likely to happen if part of the project is changed or is not completed on time. Managers of large-scale construction projects may opt for the functionality that Oracle provides. Conversely, Microsoft Project provides a more streamlined approach to CPM, with visualizations primarily through a Gantt chart. It could be the software of choice for managers in charge of smaller or less complex construction projects.
Integrating Technology with Traditional Techniques
Simulation tools, BIM and 4D scheduling software, AI and ML, and other technologies can be integrated with traditional construction scheduling techniques to provide enhanced efficiency and a greater chance of success and customer satisfaction. Indeed, many of these technologies are essential to traditional construction scheduling techniques. The tools used to create PERT charts, for example, are integral to the PERT technique.
Technologies like AI, ML, BIM, and simulation tools can be integrated into various phases within traditional construction scheduling techniques. For instance, a project manager could use BIM and/or simulation in the initial planning phase of the last planner system. Meanwhile, employing AI and ML throughout the life cycle of the construction project can yield valuable insights that can be used in daily huddles and other planning sessions to improve efficiency.
Best Practices for Effective Construction Scheduling
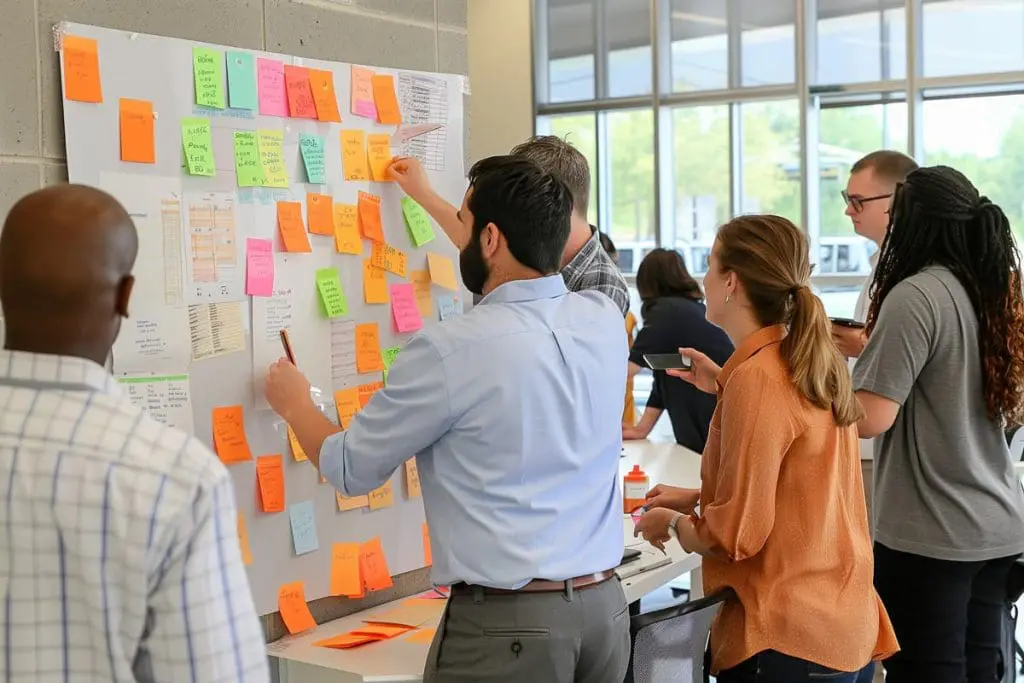
Since construction projects vary in size, scope, and complexity, it makes sense to simplify their planning as best as possible. One way to do this is to apply the following best practices, which can help construction managers on any project, no matter its size, achieve their desired goals.
Setting Realistic Timelines and Milestones
Having pre-set realistic timelines, baselines, and milestones is critically important to the success of any construction project, where success is predicated on meeting deadlines. The success of a project is measured against baseline schedules and performance management plans, with milestones typically driven by activities and durations created in the approved baseline schedule. Setting achievable timelines, baselines, and milestones prevents projects from running over budget and time.
To set realistic timelines, construction project managers should:
- Break work into smaller and easily achievable tasks.
- Refer to previous similar projects and use their task timeframes as a reference.
- Consider any potential obstacles that could impede the completion of tasks (and plan the timeframe accordingly).
Resource Management and Allocation
Effective resource management and allocation can mean the difference between a construction project that is finished on time and within budget versus one that experiences cost and schedule overruns. This process is known as “resource loading,” where hours and costs are loaded into the schedule for project control and tracking.
Resource loadingt and allocation begin in the planning phase of project scheduling. Here, project managers identify the resources they will need during construction, including labor, equipment, materials, and other assets.
Many construction scheduling tools also provide features that allow managers to track resources throughout construction by providing real-time feedback on labor hours, available equipment, and more. Managers can make adjustments to resources as needed during construction, adjusting labor schedules, ordering more materials, and taking other steps to proactively manage the schedule. They can also allocate resources to critical tasks as necessary.
Learn to align your project budget with effective resource management. Explore our complete guide to construction budgeting for winning strategies.
Overcoming Common Challenges in Construction Scheduling
While construction scheduling is exceedingly beneficial in helping all construction projects run smoothly, it’s not without its challenges. Here’s how to manage one of the most common pitfalls associated with construction scheduling—project delays.
Dealing with Project Delays
Many things contribute to construction project delays, including budget conflicts or inaccuracies, lack of communication, and a poorly defined scope of work. One of the biggest culprits behind project delays is simply poor project planning, which can include setting unrealistic timelines, not prioritizing critical tasks, and other mistakes that can back up a project.
The best way to deal with project delays is to use a construction scheduling technique to carefully plan out the scope and timeline of the project, even before breaking ground. Construction schedules provide detailed guidelines for all project work and when the work needs to be done. Having this schedule in advance can mitigate the potential for delays.
If a delay does occur, construction scheduling techniques can still help, especially if they include regular planning meetings throughout the course of the project. These meetings can provoke ideas on how to manage the delays so that they do not significantly impact the rest of the project.
Mastering Construction Scheduling for Project Success
Construction scheduling isn’t a “nice to have,” but a necessary component of successful construction project management. Adopting leading construction scheduling techniques and pairing them with the right technology can help builders keep their projects on schedule and under budget, resulting in more efficient and cost-effective builds.
Acuity has decades of experience helping organizations with construction management of projects of all sizes. We help project managers select and implement the right scheduling strategy and apply sustainable business practices, proven project management techniques, and effective cost analysis and engineering principles to help our clients create and manage construction schedules that work for their projects.
Contact Acuity to learn more about our construction scheduling services.