Why is OSHA necessary? Put simply, the Occupational Safety and Health Administration (OSHA) saves lives. Since 1970, OSHA programs have reduced work-related fatalities by almost 63% and cut workplace injuries by 40%.
Created under the Occupational Safety and Health Act of 1970, OSHA equips employers and workers with the knowledge and tools they need to ensure a safe and healthy workplace. OSHA sets and enforces employer standards and responsibilities and provides compliance assistance, education, and training to ensure those obligations are met.
This blog explores the role that OSHA plays in employee health and safety as well as resources and tools that can help you achieve OSHA compliance.
Table of Contents
OSHA Demystified: The Beacon of Workplace Safety
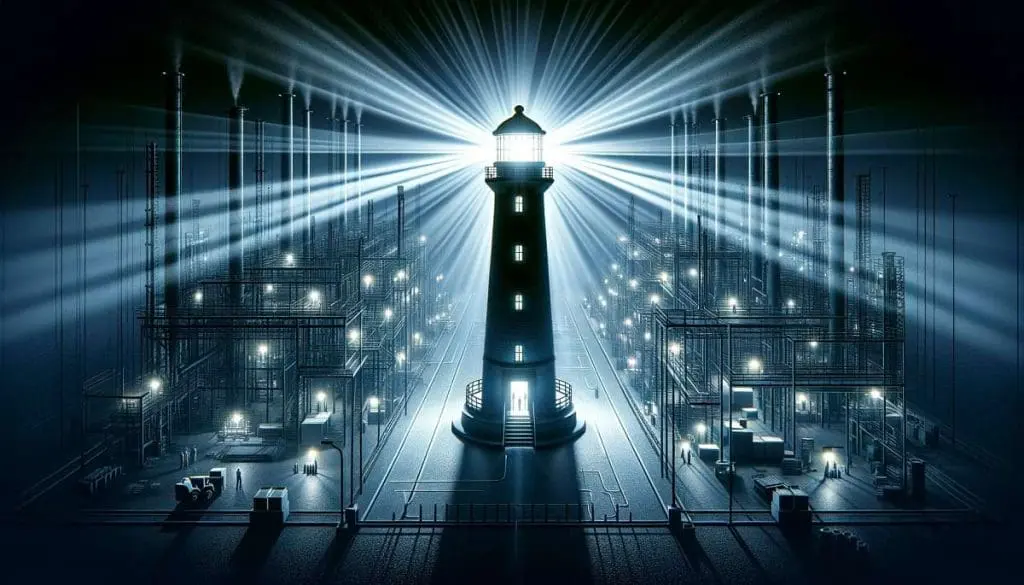
According to the U.S. Bureau of Labor Statistics, employers report 2.6 million injury and illness cases and 5,190 work fatalities a year.
OSHA requires you to safeguard your workforce, but your employees also expect you to do so. Recent survey data reveals that 75% of workers are more likely to remain loyal to a company that prioritizes their physical safety.
The Importance of Occupational Safety
OHSA’s occupational safety programs help reduce falls, slips, trips, vehicular and machinery-related incidents, exposure to chemical and hazardous materials, and more.
But OSHA also plays an important part in workplace productivity and cost management. Work-related injuries and illness are a leading cause of absenteeism, lost productivity, emotional and psychological costs, and workers’ compensation claims volume.
Proactive changes that improve workplace safety can result in significant improvements to your organization’s productivity and financial performance. According to OSHA:
- Companies spend $170 billion each year on costs associated with workplace incidents.
- Workplace health and safety programs lower injury incidences from anywhere between 9% and 60%.
- These programs can also reduce injury and illness costs by up to 40%.
The Genesis of OSHA: A Timeline of Transformation
In 1970, a staggering 14,000 U.S. workers were killed on the job – that’s 38 people every day. But these numbers were not new. For decades, thousands of workers lost their lives or faced hardship because of workplace injury and illness.
Finally, in response to pressure from labor unions, employers, and their families, in December 1970, the U.S. government passed the Occupational Safety and Health Act. In April 1971, OSHA opened its doors.
OSHA is a national agency dedicated to the basic proposition: no workers should have to choose between their life and their job.
OSHA has progressed from representing 56 million workers in 1971 to 105 million private sector workers today. These workers look to OSHA for guidance on workplace health and safety and to their employers to share information on workplace hazards and how to protect themselves.
Catalyst Events: The Urgent Calls for Change
Workplace health and safety first came under the spotlight with the Industrial Revolution and societal shifts like the formation of labor unions, civil rights, women’s rights, and the Vietnam War. However, a series of workplace tragedies and associated public outcry were instrumental in shaping OSHA, including:
- Triangle Shirtwaist Factory Fire: In 1911, 146 people were killed following a fire in a clothing factory in lower Manhattan. The factory lacked a sprinkler system, had all exit doors locked, and possessed only a single fire escape. Employees tragically lost their lives as they tried desperately to escape, succumbing to smoke inhalation, crushing injuries, or falls from windows.
- Hoover Dam Construction: The 1930s construction project caused the death of 96 workers, although unofficial reports cite dozens more fatalities.
- Texas City Industrial Disaster: In 1947, a docked freighter containing a cargo of ammonia nitrate caught fire and exploded. The blast leveled 1,000 buildings, including oil storage facilities and hundreds of homes, and killed almost 600 people. The tragedy is considered one of the largest industrial disasters in history.
- Farmington Mine Disaster: In 1968, an explosion at the Consol No. 9 coal mine in Farmington, West Virginia trapped and killed 78 underground miners. Recovery efforts continued for nearly 10 years but only 59 bodies were recovered.
Read more from the Centers of Disease Control (CDC) about the workplace tragedies that occurred before the passage of OSHA.
The Real-World Impact of OSHA: Stories from the Ground
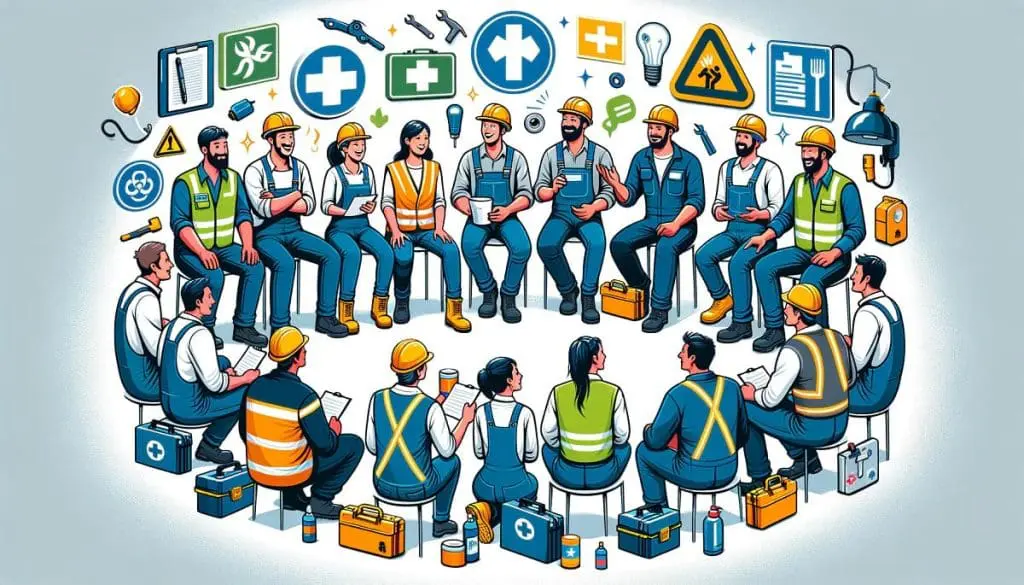
Since OSHA was established, workplace fatalities, injuries, and illnesses have been cut dramatically. OSHA proudly shares examples of success stories of OSHA-compliant employers.
Voices of Change: Testimonials and Experiences
Here are just a couple of examples of companies that have taken advantage of OSHA’s on-site consultation program and operate exemplary safety and health programs.
Lifecore Biomedical, Inc, Minnesota
Lifecore Biomedical is a fully integrated contract development and manufacturing organization focused on sterile, injectable-grade pharmaceutical drugs and medical device products. The company employs 450 workers worldwide.
Following a routine OSHA inspection in 2003, the company learned about the Minnesota OSHA Workplace Safety Consultation (WSC) Program. WSC works with employers at no cost to help them improve workplace health and safety. Based on WSC’s recommendations, Lifecore implemented several improvements including routine safety audits, fall prevention measures, a safety on-boarding process for new hires, and team-based incident and near-miss investigations.
Results: With OSHA and WSC’s assistance, Lifecore has reduced injury rates by 66% and decreased its days away, restricted, or transferred (DART) rate by 73%. Read more.
Grenzabach Corporation, Georgia
Grenzabach is a German-owned material handling manufacturer with 100 employees at its Newnan, Georgia facility. Prior to 2012, the plant was averaging five recordable injuries per week. Despite a robust commitment to health and safety, additional measures were needed.
To help identify workplace hazards, the company reached out to Georgia’s OSHA On-Site Consultation Program and Tech Safety, Health, and Environmental Services (SHES) program.
Following an on-site assessment visit, Grenzabach mitigated all health and safety issues. It also pursued OSHA’s Safety and Health Achievement Recognition Program (SHARP) certification. Small businesses that achieve SHARP status receive a deferral from OSHA or the State Plan programmed inspections for the period that the SHARP designation is valid.
Results: Since making these changes, the number of recordable incidents at the plant has decreased by 85%. In 2020, the company completed an entire calendar year with zero recordable injuries. Read more.
OSHA’s Multidimensional Approach to Safety
From proactive training to rigorous compliance checks, OSHA offers a great deal of information and assistance to employers to help them comply with their health and safety responsibilities.
The Power of Prevention: OSHA’s Proactive Initiatives
OSHA’s forward-thinking programs help employers preemptively address potential hazards. Tools and resources offered by OSHA include:
- Guidance on establishing a safety and health program.
- Compliance assistance specialists.
- No-cost on-site safety and health consultation services for small businesses.
- Cooperative programs: Businesses, labor groups, and other organizations can work with OSHA to prevent fatalities, injuries, and illnesses in the workplace.
- Occupational safety and health training.
- OSHA educational materials.
OSHA and Healthcare: A Critical Intersection
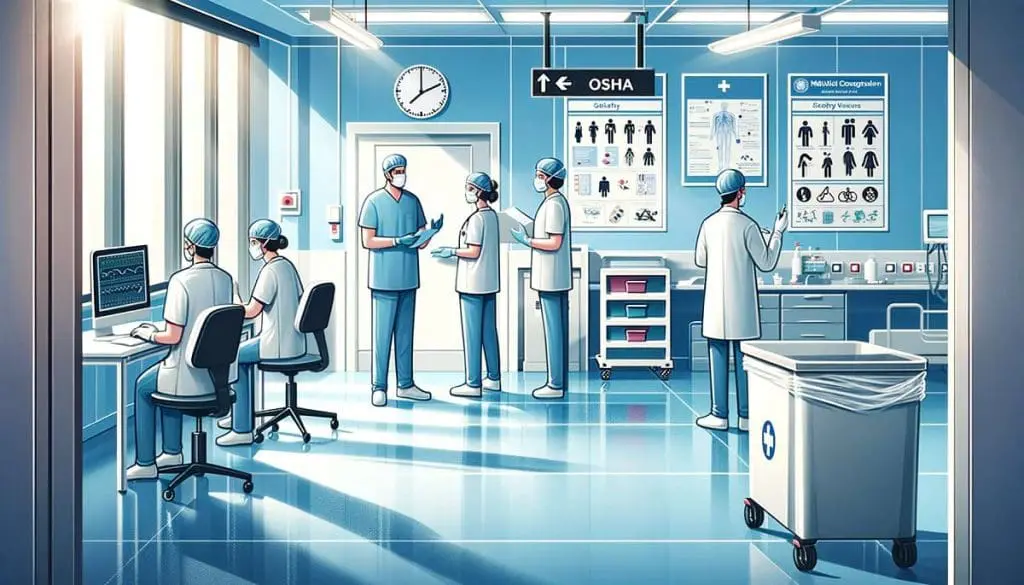
According to OSHA, more workers in the healthcare industry are injured than in any other. In 2020, the sector reported a 40% increase in injury and illness cases.
Healthcare workers face many safety and health hazards including airborne and bloodborne pathogens, chemical and drug exposures, waste exposures, ergonomic risks such as repetitive and heavy lifting tasks, workplace violence, and more.
In addition to being dangerous, these injuries come at a high cost to employers. Nationwide workers’ compensation losses result in a total annual expense of $2 billion for hospitals.
For these reasons, OSHA has developed specialized standards for healthcare that include safety and health management systems, safe patient handling, and workplace violence.
Navigating the Healthcare Labyrinth: Best Practices for Compliance
Because of the high-risk nature of this sector, OSHA offers a range of tools and resources to help hospitals and healthcare employers align with OSHA standards. Check out OSHA’s Worker Safety in Hospitals website for information including:
- Tools for assessing and advancing a culture of safety.
- A “How Safe is Your Hospital?” questionnaire and safe patient handling assessment.
- Facts about who is most at risk and what hospitals can do to address the problem.
- How health management systems work, save money, and improve quality of care.
- A roadmap for preventing workplace violence.
- And more
Acuity International & OSHA: Pioneering a Safer Tomorrow
Acuity International is committed to championing OSHA standards. Whatever industry you’re in, we can deliver tailored, one-stop occupational health services – whenever and wherever those services are needed.
Our innovative and diverse occupational health services include pre-placement, medical, return-to-work, fit-for-duty, and wellness exams, as well as drug and alcohol testing, respirator fit testing, injury prevention services, COVID testing, vaccinations, and more – delivered via mobile and onsite options.
These cost-effective solutions are backed by robust, centralized health analytics for ease of case management, including real-time exam tracking and reporting, data management and transmission, physician medical review services, and more.
FAQs: Unraveling the Essentials of OSHA
Why is OSHA necessary?
In 1970, approximately 14,000 workers were killed on the job – about 38 every day. Today, thanks to OSHA’s standards, enforcement actions, compliance assistance, and other programs, thousands of lives have been saved and countless injuries and illnesses prevented.
OSHA also supports workplace productivity and cost management. OSHA’s workplace safety programs lower injury incidences from anywhere between 9% and 60% and workplace safety programs can reduce injury and illness costs by up to 40%.
Why is OSHA important to employees?
According to OSHA, each year more than 3.2 million workers suffer a serious job-related injury or illness.
OSHA cites numerous examples of real stories where workers were killed or injured at work due to a failure by employers to comply with OSHA standards – and how these cases could have been prevented.
OSHA safety and health standards assure safe and healthful conditions for workers. To date, OSHA and its state partners have reduced work-related fatalities by almost 63%.
What are the pros and cons of OSHA?
OSHA provides vital guidance, standards, and assistance for health and safety in the workplace. However, OSHA compliance can be challenging. Health and safety standards vary by industry and even employers who passionately advocate for a safe and healthy workplace often struggle to identify gaps in their OSHA program.
OSHA penalties for non-compliance can also be strict. A serious violation can result in a $15,625 fine. Failure to abate is $15,625 per day beyond the abatement date, and willful or repeated violations is $156,259 per violation. States with their own OSHA programs must also adopt maximum penalty levels that are at least as effective as the federal government’s OSHA.
The Undeniable Necessity of OSHA: Reflecting on Why OSHA is Necessary for the Future of Occupational Safety
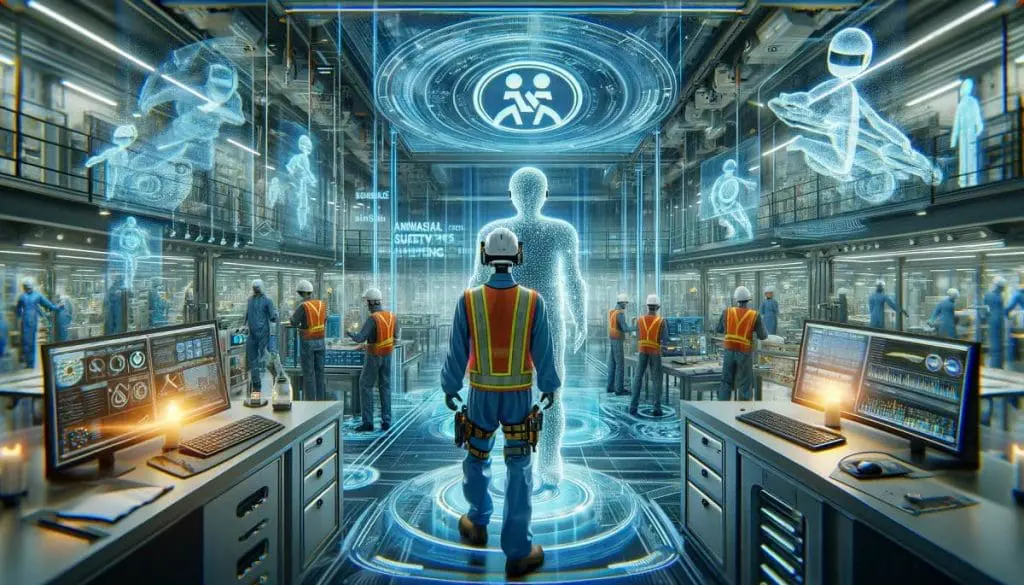
OSHA is a necessity to aid in the prevention of workplace fatalities, injury, and illnesses. But an OSHA-compliant workplace is also sound business. OSHA programs reduce costs related to injury and illness. Prioritizing occupational safety also gives you a recruiting edge, decreases absenteeism, increases productivity, and enhances employee satisfaction.
OSHA has overseen dramatic improvements in workplace safety over the last five decades, and in a post-COVID pandemic workplace, OSHA’s role is more important than ever.
Learn how Acuity’s occupational health services can help you maintain a healthy, safe, and productive workforce and stay OSHA compliant.